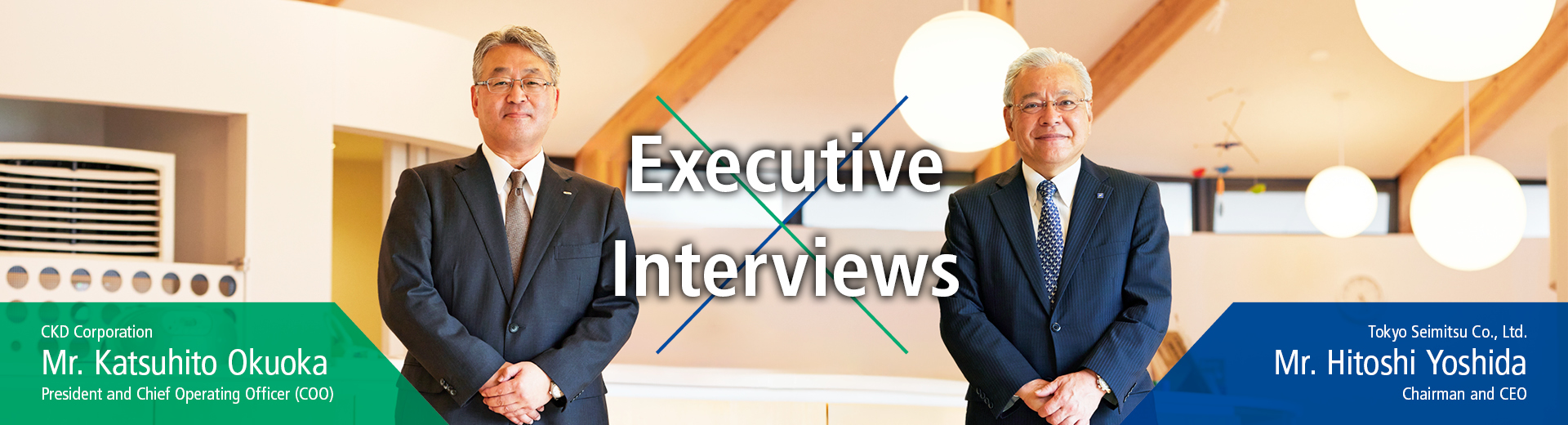
About President Okuoka
School days
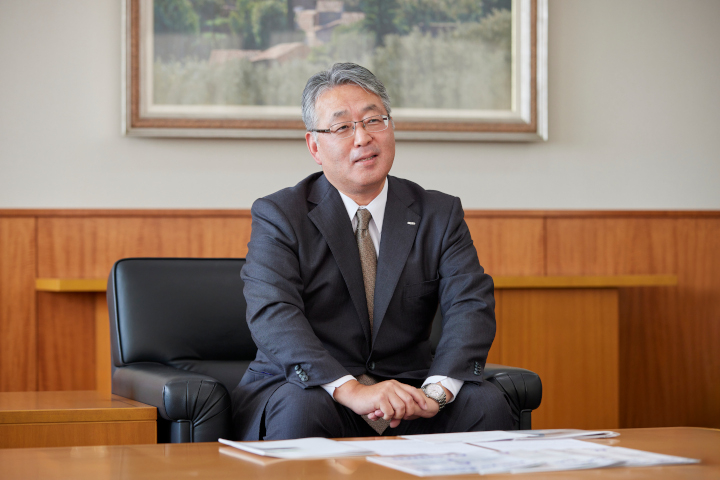
Yoshida
President Okuoka, could you tell us about when you were a university student?
Okuoka
As a native of Nagoya, I went to a local university and majored in electrical and electronic engineering. I recall doing experiments with a group of friends in a relaxed atmosphere. But what I remember more than my schoolwork is the ski trips I took with friends almost every week during the winter season and playing pool in the off season.
Job history after joining the company
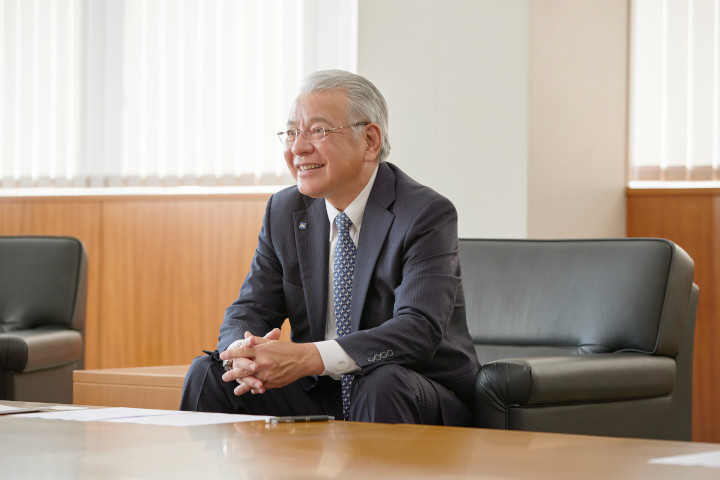
Yoshida
What kind of job have you had since joining the company?
Okuoka
After joining the company, I worked as an electrical designer for production engineering in the in-house team developing automated machinery and other equipment.
With the system we used at the time, we were unable to convey all the details of orders to the production side. In order to communicate information directly to the plant, we embarked on some efforts that had never been made in our company, on automated machinery in particular. For example, we developed a machine that allows you to set up a test immediately after reading a barcode.
Yoshida
There is a growing trend of automation today. You were at the leading edge of that trend at the time.
Okuoka
I guess that, back then, our company was lagging behind in automation like others. So, we thought we should focus on what we were lagging behind in.
After that, I got interested in mission-critical systems. When I engaged in a product transfer project, I switched from production engineering to production management. And I went on to move to the plant management department. Then, I moved to planning departments such as production planning and business planning. After working on mission-critical systems temporarily while engaging in planning, I served as division chief and then worked in the headquarters. And that has brought me to my current position.
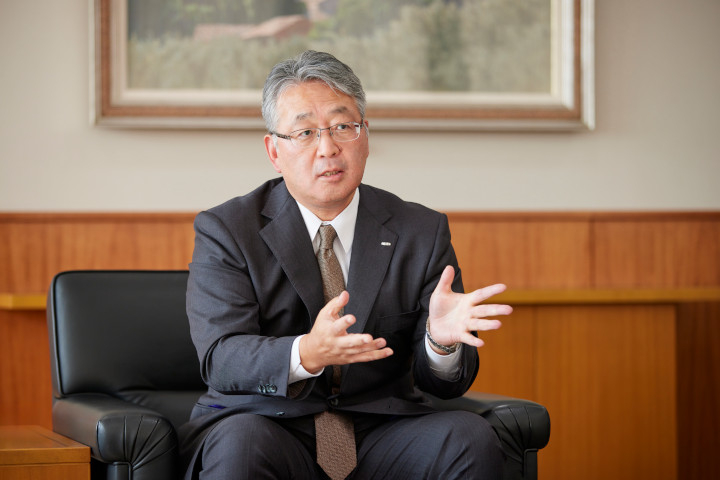
Yoshida
You said you engaged in production management. Did you experience with introducing an ERP system?
Okuoka
Yes, we introduced SAP about five years ago. It was not an easy task.
The production management system we had at the time was tailored to our style of manufacturing. Now, we had to standardize data in order to adjust our manufacturing style for ERP. Let me use an analogy of clothes to explain it. You have always worn made-to-order suits, but you suddenly need to put on a ready-made suit and you have to slim down your body. Some of the employees opposed the reform, and I had a hard time persuading them.
The bigger trouble came when problems with the system and data occurred after we switched to ERP, causing significant delays in delivery and throwing us into chaos. To deal with these problems, I kept visiting all our plants without any days off from the year-end and new-year holidays until after the Golden Week holidays in May. Every employee involved in this project worked so hard, and it was good to see teamwork mentality develop among them. Soon after we introduced the SAP system, we had significantly delayed deliveries, causing inconvenience to our customers. I was deeply grateful for the support of the sales department staff who have built trusting relationships with the customers through their daily activities.
Yoshida
You overcame a tremendous hurdle. We also introduced ERP several years ago, and we had a hard time, too. Customizing ERP to adapt to our existing system would cost money. So, we tried to adapt our business processes to ERP, which turned out to be quite difficult. Every department spent a year identifying problems, by running our existing system and the ERP system at the same time for testing. There was no major confusion when we put the ERP system into operation, but the testing process took an enormous number of person-hours.
Your company’s ERP system remains in stable operation, doesn't it?
Okuoka
The increased accuracy of our system’s data is now our weapon. If we enter correct inputs, we will certainly get correct outputs, which allows us to understand data easily and accurately. I think it also helps us make management decisions quicker.
About Strengths and “Creating Solutions Together”
CKD Corporation's strengths
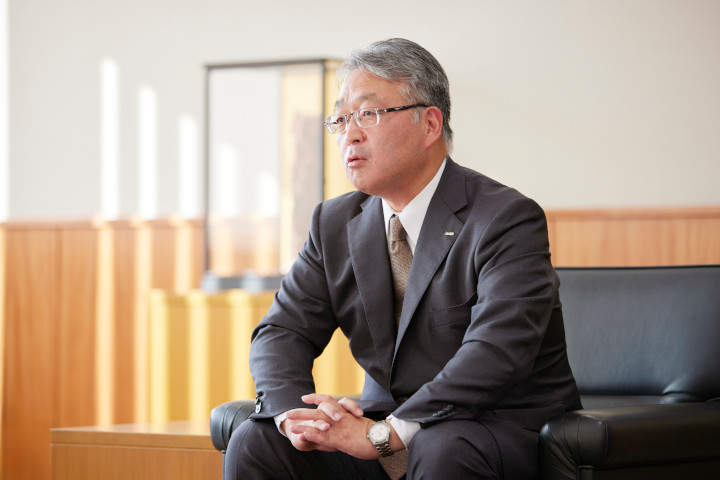
Yoshida
Could you tell us about what you value in products and services and your strengths?
Okuoka
We pursue the same values for both our automatic machinery and component products, which are high accuracy, high durability, and cleanliness. I always tell people that these represent what we value in our products.
Rather than selling in large quantities at low costs, we are focused on solving our customers’ problems one by one in a systematic fashion, by combining component products, such as pneumatic equipment, electric equipment, and fluid control equipment. Based on the notion that highly durable products reduce waste and help customers increase productivity, which is good for society, we have developed ultra-high-durability pneumatic components, building on the basic technology.
Yoshida
That’s great. Personally, I think that’s what is important about Japan’s monozukuri. Japan’s monozukuri is characterized by high quality and safety. We want to stay committed to providing safe products. As a manufacturer of measuring instruments, we always think about what to do to make sure our products deliver accurate measurement results.
Okuoka
That’s what we all should focus on. Otherwise, we will not be able to survive.
Brand slogan
Yoshida
Could you tell us also about the brand slogan you created this year?
Okuoka
This year marks the 80th anniversary of the foundation of our company, and we wanted to create something that employees could empathize with. Our company was originally established as a nation policy concern with investments of five major companies to manufacture parts for fighter planes. There was no founder’s philosophy. So, we decided to define our purpose and create our brand slogan. We built a branding project with the participation of all generations of employees, both at home and abroad and both men and women. And, in a vote by all employees, “Creating Solutions Together” was selected from among three final candidates.
It reflects our determination to pursue automation technology and promote co-creation further, as well as to bring about a richer future by solving environmental and social issues, through creativity and innovation in collaboration with customers, business partners, and CKD employees. I think we should stay committed to this brand slogan.
Yoshida
It will be great that, when your company marks the 100th anniversary, employees of the future will appreciate the decision that the president serving at the 80th anniversary made to create this brand slogan.
Sustainability initiatives
CKD Corporation's sustainability initiatives
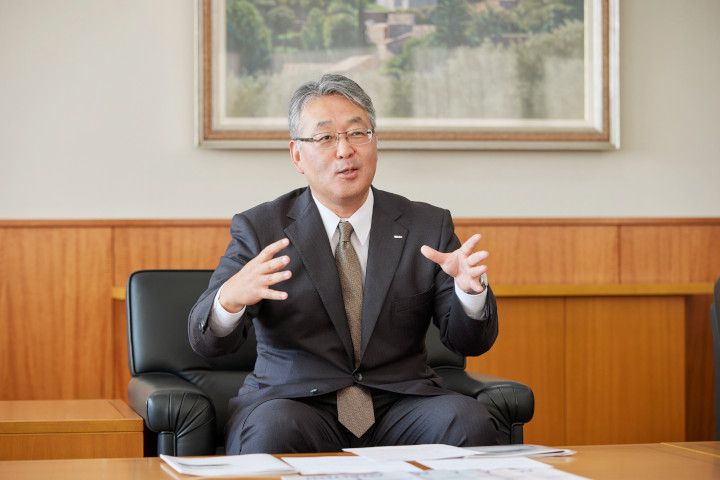
Yoshida
What is your company doing to achieve sustainability?
Okuoka
There are several initiatives we are pushing forward as part of our business.
One of the SDGs we are addressing is “Affordable and Clean Energy,” which corresponds to winding machines for lithium-ion batteries. The goal of “Good Health and Well-being” corresponds to pharmaceutical packaging systems and life science components.
And the goal of “Gender Equality” corresponds to pneumatic balancers. Assistive devices make heavy objects light enough for women and elderly people to do jobs that require physical labor.
Also, as part of the initiative for the goal of “Zero Hunger,” we are engaged in smart agriculture, with plastic greenhouses built on our plant premises. This initiative involves developing systems, such as an application that allows farmers to control farming activities remotely. For example, such an application will enable farmers to open watering valves remotely. Our shared ultimate goal is to “ensure farmers can take days off.” I think that factory automation technology can also be applied and contribute to the primary industries such as agriculture and fishery.
Yoshida
That may lead to future business opportunities.
Okuoka
Putting aside profit making, these initiatives make it easy for employees to see that they are contributing to society through technology. I think that, once this is understood by all employees, they will become more motivated and willing to engage.
Yoshida
That’s good. I find your ESG-based development initiatives very useful.
Decarbonization
Yoshida
Is there any activity you are particularly focused on in terms of decarbonization?
Okuoka
In addition to initiatives related to products, we are making efforts to switch to more productive equipment and LED lamps and install solar power generators. Also, we have introduced green electricity to the plant where we manufacture highly durable component products. Year by year, we are stepping up efforts not to emit CO2 in the course of manufacturing as well.
We have two CO2 emissions reduction targets. One is to cut the real total CO2 emissions by half in 2030 from the FY2022 level. The other is to half the CO2 emission intensity from the FY2013 level. We are also working to meet the government’s goal of achieving net zero CO2 emissions by 2050.
Internal programs for employees
Yoshida
What about internal programs for employees?
Okuoka
My predecessor worked really hard to implement such programs. So, I have been doing my best to carry on those programs. At the onset of the COVID-19 pandemic, we set up a crisis management committee to review our work styles, embracing new work arrangements such as teleworking, staggered working hours, and temporary permission for commuting by car. After introducing these arrangements, we saw our productivity increase. Employees with small children use these work arrangements as they see fit for their work, and we still have the teleworking system in place.
We also have an on-site day-care center on the left just after the main gate of our headquarters building. This day-care center symbolizes our commitment to pursuing diversity. When we discussed where to build the day-care center, the then chairman was adamant that it should be located in front of the company building. So, we built it right next to the main gate. Now, employees are happy with this idea of building a day-care center near the main gate, because, whenever something comes up, they can readily check on their children they entrust to the center. We are also seeing an increasing number of competent women join our company.
About the relationship with measuring instruments
What CKD wants from measuring instruments
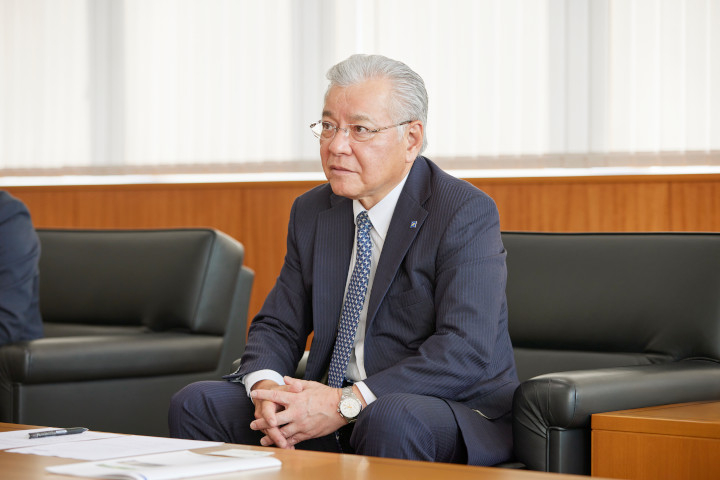
Yoshida
Your company uses a lot of measuring instruments from us. We appreciate your loyal patronage. Could you tell us about what you want from measuring instruments and how you use them? And, what do you think you will need in the future?
Okuoka
I tell people that our strengths are high accuracy and high durability, which we could not deliver without measuring instruments. Whenever we evaluate a developed product, we use your measuring instruments. They support our technologies. We develop and manufacture components and control the quality of those components. In the event of an unexpected problem, which I think should not happen in the first place, we analyze the problem to maintain trust. All of this depends on measuring instruments. None of this is possible without them.
Yoshida
Being the CEO of a measuring instrument manufacturer, I am very flattered to hear that.
You have purchased many different types of measuring instruments since long ago.
Okuoka
When it comes to measuring instruments, we have a really long relationship.
In the mid-1980s, your company purchased our valves for your semiconductor manufacturing equipment, but those valves were defective. Your engineers gave us advice and worked together with our engineers to improve the durability of our valves. During this process, they measured valve durability using your measuring instruments and, based on the advice from your engineers, succeeded in developing valves strong enough to withstand 10 million durability tests for the first time in Japan.
Hearing this behind-the-scenes story from our salespeople before this interview brought home to me the trouble our defective valves caused to you and that your technical know-how has been indispensable for the high durability that we boast today. I talked feelingly about these things with them.
Yoshida
I didn’t know about it. Your pneumatic and fluid control equipment is the vital base for our instruments. I hope the two companies will keep working together going forward.
Purchase of the X-ray CT system
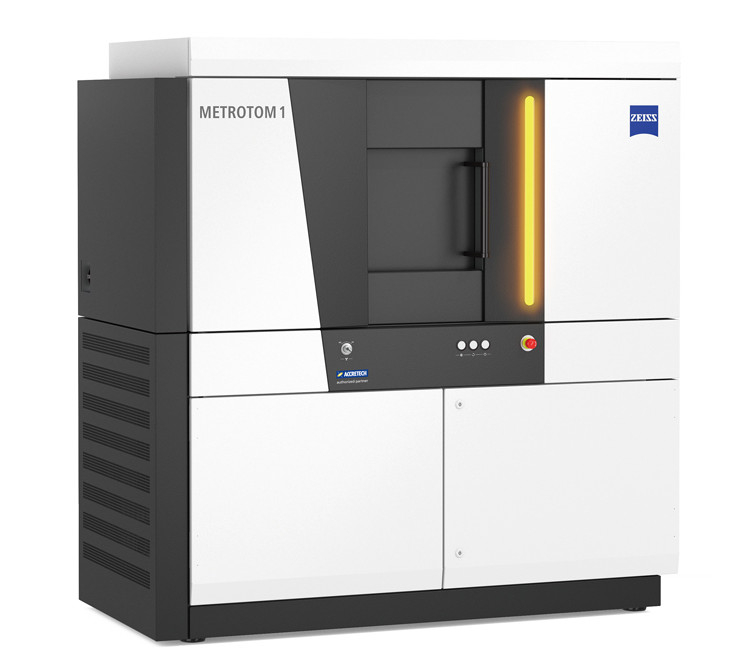
Yoshida
You purchased our X-ray CT system in 2023. What did you buy it for?
Okuoka
When we measure the dimensions of the most critical functional part of a valve, we cut the part and measure its cross section. And that involves 12 processes. The X-ray CT system we bought from you reduces the number of processes to just one, saving us three days’ worth of labor. I was also told that the system only takes one-third the space.
Yoshida
We will be happy to do our best to help you achieve the results you want. Any request will be welcome.
Expectations for Tokyo Seimitsu
Yoshida
What do you expect from us?
Okuoka
We expect a lot from you. The materials we handle are in the form of gas or fluid. So, I would like to see you try aggressively to develop products that can handle things that have been invisible or impossible to measure in the past. Also, it will be nice if we have a product that allows us to take a close look at the state of junction or adhesion.
Yoshida
We are doing our best every day to make it possible to evaluate what has been invisible in the past. We will introduce new products to you as they become available.
Future challenges and prospects
CKD Corporation's future prospects
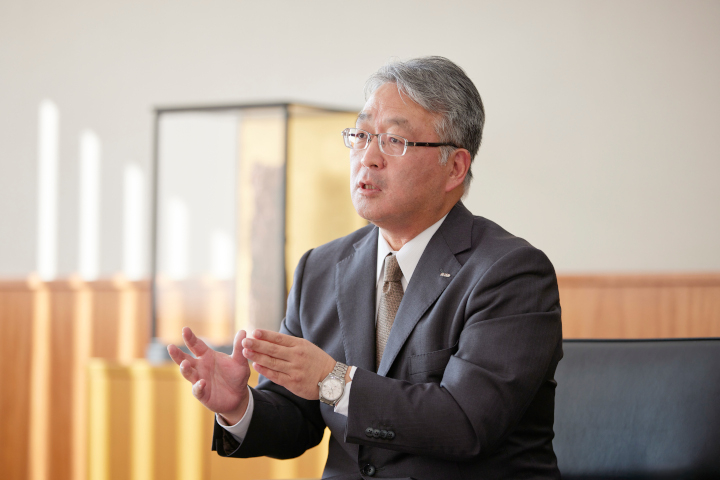
Yoshida
Now, the world of manufacturing seems to be changing drastically. Could you share your future prospects?
Okuoka
I think that automation will advance to address labor shortages and that the use of EVs and other electric-powered products will grow to protect the environment. I also expect that society will shift from mass-production, mass-consumption economy to circular economy. We would like to propose solutions to customers to address each of these social issues.
On the environmental front, I think we should focus on semiconductors and lithium-ion batteries and other secondary batteries, which are indispensable for GX and DX, as well as on the use of hydrogen for decarbonization. We are also going to focus on electric component business because many customers are shifting from pneumatic equipment to electric equipment.
To help customers solve their problems, we will offer our products as units or systems, rather than selling them one by one. Our aim in providing products as units or systems is to expand business opportunities in maintenance as well.
Yoshida
Hearing your talk, I feel that your situation is very similar to ours.
This is about our precision measuring instrument business. In the past, measuring instruments have been used in the laboratory. But, now, plant personnel are beginning to use them on production lines to improve the quality of production. And that requires automation. We also see automation as a keyword. We provide you with sensors and other devices to achieve automation, and it will be exciting to see these products used in combination with your automation system.
Previously, many of our measuring instruments were intended for internal combustion engines of automobiles. But, with the auto industry making a big shift to EVs, we have been working on charge and discharge test system for batteries, and automation is required in this area as well. You said you also want to try many things with regard to batteries. It will be wonderful if we could work together in approaching the battery industry.
Okuoka
Yes, they are the preceding and succeeding processes. We will be happy to cooperate with you.
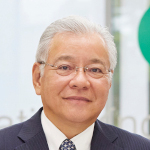
Tokyo Seimitsu Co., Ltd.
Chairman and CEO
Hitoshi Yoshida
April 1983
Entered Tokyo Seimitsu Co., Ltd.
April 2002
Executive Officer, Metrology Company
Leader of the General-Purpose Measurement Group
April 2005
Managing Executive Officer, Metrology Company
June 2005
Appointed as Director
April 2015
Appointed as President and CEO
April 2022
Appointed as Chairman and CEO (current position)
2016
Awarded the ND Marketing Award
2020
Appointed as Chairman of the Japan Precision Measuring Instruments
Manufacturers Association (current position)
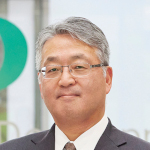
CKD Corporation
President and Chief Operating Officer (COO)
Katsuhito Okuoka
April 1991
Entered CKD Corporation
October 2008
General Manager, Production Control Department, Komaki Plant - General & Control Equipment, Production and Engineering Division"
June 2015
Executive Officer, General Manager, Components Business Division
June 2016
Director & Executive Officer, in charge of Quality and Safety
General Manager, Components Business Division
June 2018
Director & Managing Executive Officer, in charge of Quality Management
General Manager, Components Business Division
June 2019
Representative Director and Senior Managing Executive Officer, in charge of Quality and Environment, General Manager, Components Business Division
June 2020
Representative Director and Senior Managing Executive Officer, in charge of Administration, General Manager, Corporate Planning Department
June 2021
President and Chief Operating Officer, in charge of Administration
June 2022
President and Chief Operating Officer (COO)(current position)
CKD Corporation
CKD Corporation was established in 1943 under the name of “Japan Aircraft Electric Co., Ltd.”The company develops and produces automation machinery and pneumatic and fluid control equipment based on automation technology to automate manufacturing processes and fluid control technology to control fluids such as water, air, gas, steam, and oil.The company's equipment is used in a wide range of manufacturing sites, including semiconductors, automobiles, pharmaceuticals, and food products, supporting manufacturing around the world.
Products