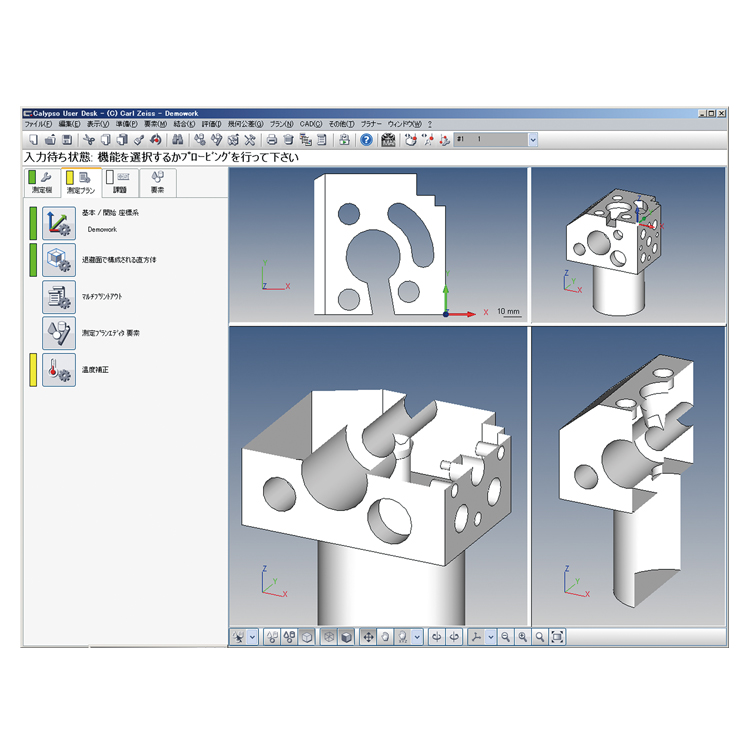
ZEISS CALYPSO
ZEISS CALYPSO is one of the most highly evaluated coordinate measuring machine software applications in the world. A CAD kernel ensures unmatched operability, which combined with powerful features of software that is designed to bring you the ultimate in versatility and performance.
Features
Improved AI Function
The AI function includes three algorithms for automatic element recognition, automatic coordinate system setting, and automatic measuring plane recognition while assisting operators. The AI function supports not only points, straight lines, flat surfaces, spheres, symmetrical points, circles, and cylinders but also cones, ellipses, square holes, and long holes without the need to select the element types before measuring. Simple operation procedures enable successive measurements from measuring one of the elements at random points to pressing the “Terminate” button to stop element measurements.
Automatic Geometric Element Recognition
Our own measuring method and recognition algorithms (patented in Japan and overseas) enable automatic recognition of geometric forms by the direct measurement (probing) of a workpiece. This dramatically reduces procedures to input measuring items.
Automatic Coordinate System Recognition
Measured geometric elements and items required for coordinate system settings (spatial compensation, rotational compensation, origin) are determined automatically and these settings are configured.
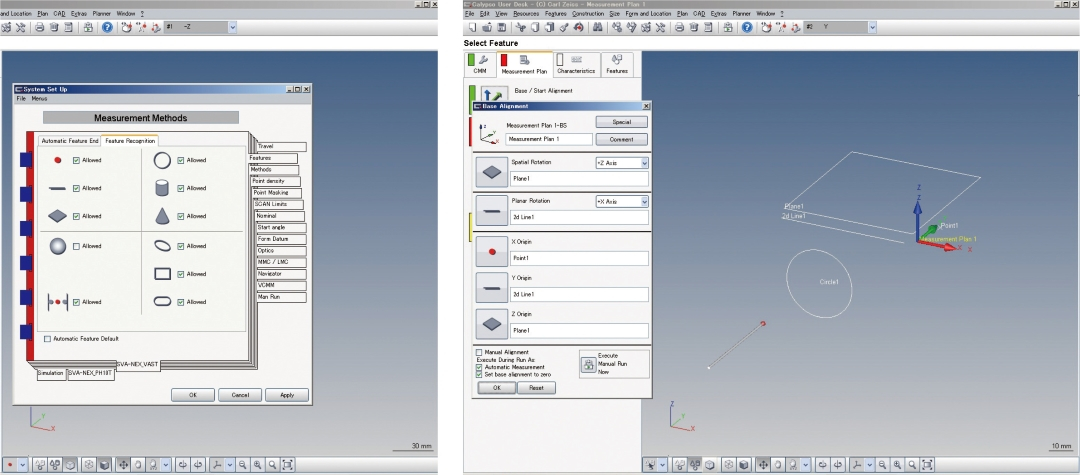
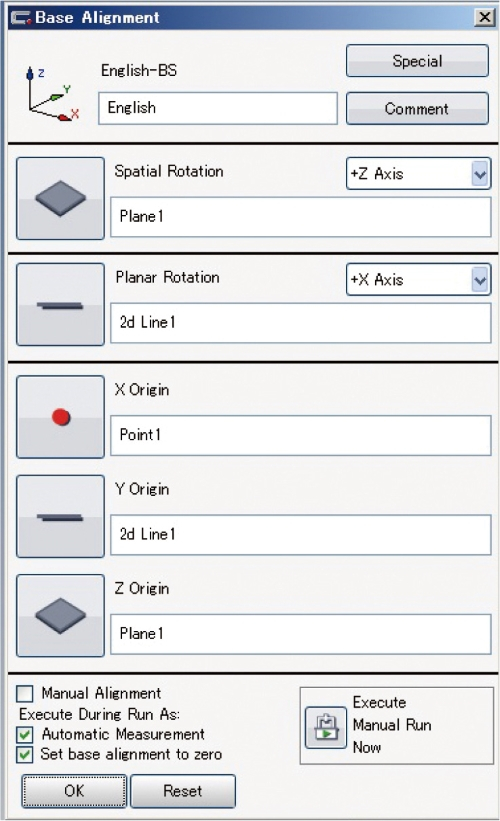
Automatic Generation of Measuring Path
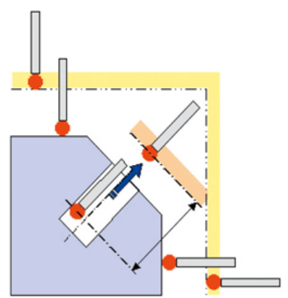
ZEISS CALYPSO’s safety plane philosophy eliminates the need to input probe path points (intermediate points). Once the bypass boundaries (area around the workpiece) are specified, the probe automatically moves on the safety plane so it does not interfere with the workpiece. For movement on the same surface, another safety plane can be configured to make the amount of movement smaller.
The measuring path is generated automatically in accordance with safety plane, supplementary safety plane, number of measuring points, and probing return distance. Measuring path points and probing points can be specified arbitrarily within and between measuring elements, which allows the operator to create the most appropriate measuring path.
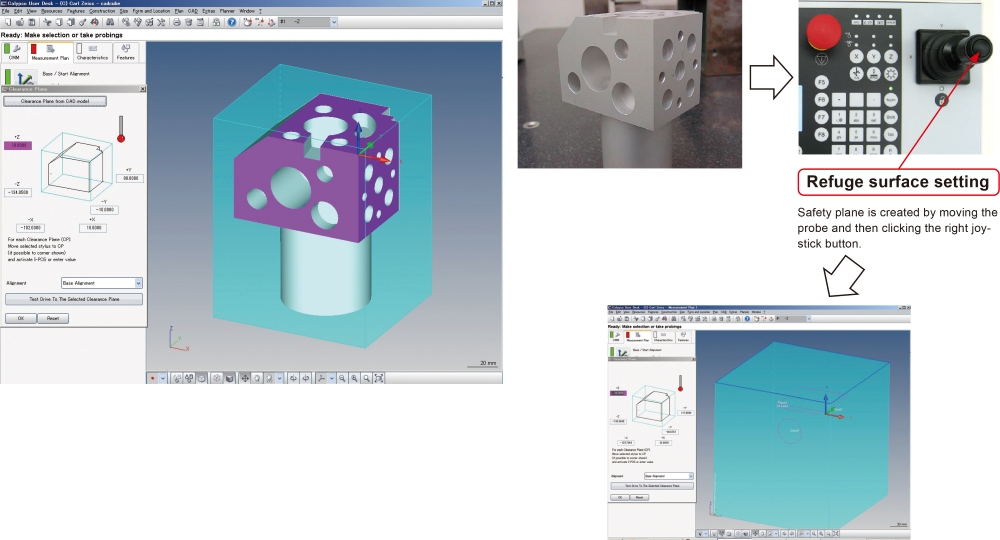
On-screen Probe Angle Simulator (For Articulating Probe Head)
An operator may wonder whether the probe is oriented correctly after specifying an orientation such as A-axis:0˚, and B-axis: -90˚. The on-screen probe angle simulator provides a screen image of the probe positioned at the input rotation angle and the inclination angle, so the operator can confirm that the desired result has been attained. When CAD data is available, clicking an element automatically changes the ideal probe orientation based on the normal information. This function becomes especially helpful in the case of inclined holes and inclined axes. Even when CAD data is not available, the orientation of the probe can be changed automatically to the normal direction relative to the actually measured projection plane. An operator used to input the rotation angle while inspecting the workpiece and plans considering interference with the stylus. With the on-screen probe angle simulator, rotation angle settings become simpler than ever before. The stylus simulation function option is required.
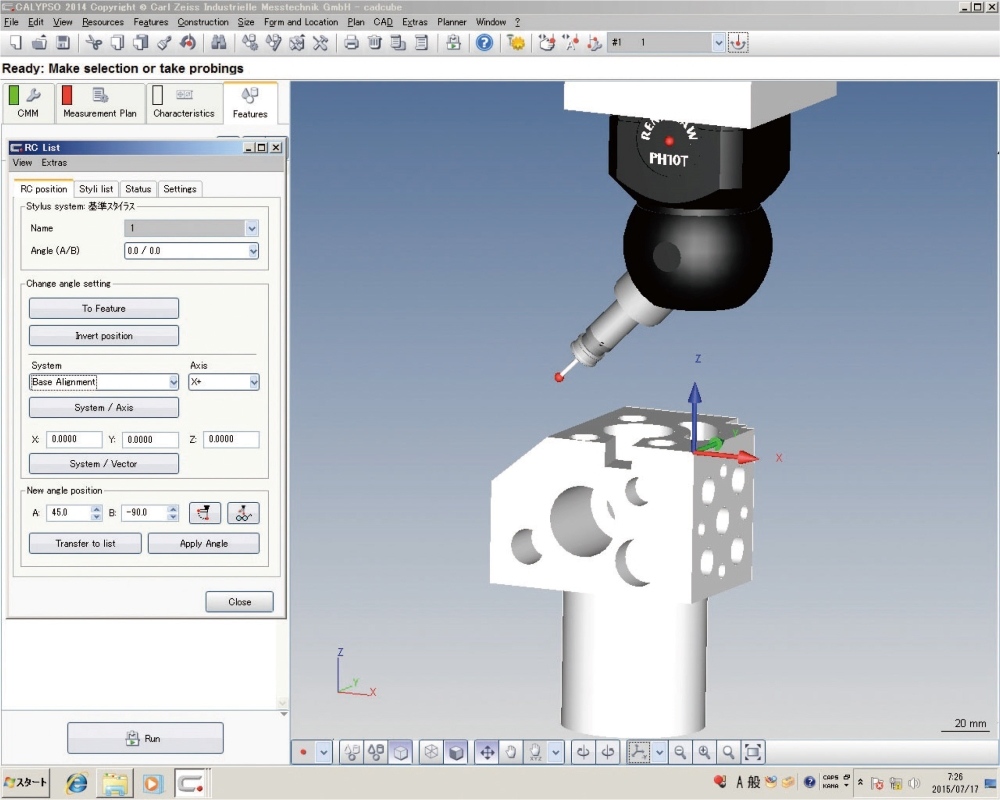
Intuitive operation made possible with the ZEISS CALYPSO for use with X-ray CT
ZEISS CALYPSO, the software for the coordinate measuring machine, can be used for evaluations in the X-ray CT system, ZEISS METROTOM 800/1500. This software achieves consistency and compatibility with all the ZEISS systems (the coordinate measuring machine, the X-ray CT system, and the sensors). Users who are already using the ZEISS CALYPSO can use measurement plans created with the measurement device they are currently using as is in the X-ray CT system ZEISS METROTOM 800/1500, and without any additional training. Furthermore, by selecting geometric elements in a CAD system, it is possible to create measurement plans intuitively offline. In the ZEISS METROTOM 800/1500, the preparation process up to measurement can be made efficient with a familiar user interface.
In addition, in the ZEISS CALYPSO, errors between actual measurement and design value at measurement points are displayed in color gradations (standard feature). It is possible to visually confirm the error of each actual measured value obtained for evaluation of flatness, roundness, and cylindricity.
The CT data evaluated in ZEISS CALYPSO are gathered and accumulated in ZEISS PiWeb and managed centrally. It is possible to statistically analyze the accumulated data, create a graphical report, and monitor the measured results.
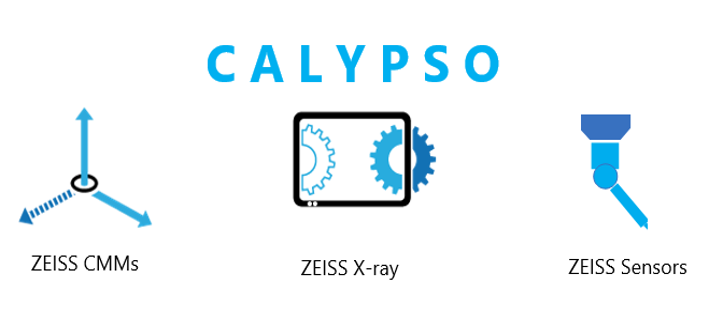