Chemical Substances Control
With regard to the chemical substances, the Tokyo Seimitsu Group uses and that are contained in component materials, the Group complies with the laws and regulations of Japan and of the regions to which it exports. For chemical substances that are not regulated, we perform management based on voluntary standards to minimize impacts on people and the environment.
Eco-Factory
Chemical Substances Control Based on Voluntary Standards
In our internal regulations, we stipulate substances with the potential to pollute the environment, and mandate notification to the person responsible for environmental management when handling such substances. In addition to keeping track of the amount of each substance handled, storage location, maximum storage volume, etc., we have SDSs*¹ and emergency response tools, conduct periodic drills to prepare for emergency situations, and are promoting the use of non-toxic or low-toxic alternatives to organic solvents and other hazardous chemical substances. In fiscal 2023, we reduced the number of chemical substances by 13 compared to the reduction target of 10 substances.
We also conduct chemical substance risk assessments*² when considering purchases or making changes in operations. In fiscal 2023, 118 chemical substance risk assessments were conducted for newly adopted chemicals and to review chemicals already in use.
*¹ Safety data sheets (SDSs)
Provide information on the hazards, toxicity, storage, disposal methods, and other information on the handling of chemical substances. In accordance with SDS management regulations, we regularly review safety data sheets and update ledgers when we handle applicable chemical substances in our departments, and share the updated information internally under the management of the Quality Assurance Department. In addition to regular reviews on an annual basis, SDSs are reviewed as appropriate when legal revisions or other changes are made.
*² Chemical substance risk assessments
Assessments conducted to identify the dangers and hazar ds of chemical substances and their formulations, estimate the degree to which they may cause danger or health problems to workers, and consider measures to reduce the risks. In accordance with our chemical risk assessment implementation management regulations and management standards, we take measures based on the Industrial Safety and Health Act and take necessary measures to prevent danger or health problems to workers.
Chemical Substance Risk Assessment Implementation Requirements
When the relevant department newly adopts or changes raw materials, etc. that are chemical substances, etc.
When the method or procedure of work related to manufacturing or handling of chemical substances has been newly formed or changed
When there has been or is likely to be a change in the level of danger or toxicity of an applicable chemical substance
When the work environment has been changed (relocation of workplace, etc.)
Chemical Substance Risk Assessment Procedure
(1)
SDS confirmation
(2)
Identification of operations that use chemical substances, etc., and confirmation of processes and procedures
(3)
Identification of hazards and exposure level
(4)
Risk estimation
(5)
Consideration of risk reduction measures
(6)
Implementation of risk reduction measures
(7)
Chemical substance risk assessment are summarized in the Chemical Substance Risk Assessment Implementation Table and submitted to the Maintenance Section of the General Affairs Department
(8)
After confirming the content of the submitted chemical substance risk assessment, the Maintenance section of the General Affairs Department makes a decision on the purchase and use of the applicable chemical substance
SDS Management Flowchart
Management is carried out according to SDS management regulations based on plant standards.
Using SDSs, we share what we are aware of regarding the dangers posed by the items we ship and the substances that we handle.
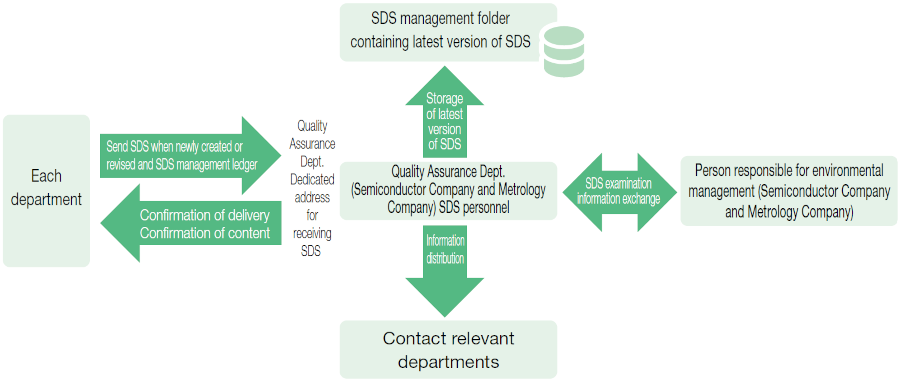
Specified Chemical Substance Control (PRTR)
We are promoting the reduction and substitution of chemical substances in accordance with the PRTR* Act, Ordinance on Prevention of Organic Solvent Poisoning, and the Poisonous and Deleterious Substances Control Act. Of chemical substances that we handle, we have submitted notifications for two substances that exceed standard amounts for substances specified by the PRTR Act and five chemical substances to be appropriately controlled according to the Tokyo Metropolitan Environmental Security Ordinance.
* The Pollutant Release and Transfer Register (PRTR)
It is a system for identifying, compiling, and publicly announcing the sources of hazardous chemical substances and the amounts released into the environment
Amounts of Pollutants Subject to the PRTR Act Released
(Unit: tons)
FY2019 | FY2020 | FY2021 | FY2022 | FY2023 | |
Amount released into the atmosphere | 0.0 | 0.0 | 0.0 | 0.0 | 0.0 |
Amount released into bodies of water |
0.0 | 0.0 | 0.0 | 0.0 | 0.0 |
Amount transferred as waste |
11.2 | 9.4 | 11.1 | 11.0 | 10.0 |
Locations covered: Hachioji Plant, Hanno Plant, and Tsuchiura Plant
Control of Chemical Substances Contained in Products
Our Basic Environmental Policy states that we will carry out efforts to “make continuous improvements in order to reduce environmental impact,” “prevent pollution,” and “comply with environmental laws and ordinances related to business activities.” In order to establish a system for managing chemical substances contained in products in response to environmental laws and regulations and customer requirements, the Group has established the Environmental Green Initiative Team within the Sustainability Department. The Environmental Green Initiative Team conducts briefing sessions for suppliers to request strict control and reporting related to chemical substances contained in the parts we procure. So far, over 400 suppliers have participated. It has also conducted cloud-based surveys for suppliers on the RoHS Directive, REACH, and other topics. We also have an analysis room equipped with an X-ray fluorescence spectrometer, gas chromatograph mass spectrometer, and other equipment, and have established a system that allows us to perform checks as needed.
Green Procurement
In April 2003, we established our Green Procurement Guideline and have received cooperation from our suppliers in our efforts to manage chemical substances in products. As regulations on the management of hazardous chemical substances have become more stringent in recent years, in fiscal 2023, we established the Green Procurement Standards, which have strengthened the Guideline, and are working to build a system that prioritizes the procurement of environmentally- friendly parts and materials with low environmental impact.
Compliance with RoHS Directive and Other Environmental Laws and Regulations
For the Metrology Company products, we have investigated six substances of the RoHS Directive and the four phthalic acids added in 2021, determining that 100% of our products are compliant. While Semiconductor Company products are exempt from the RoHS Directive as large-scale stationary industrial equipment, we established a RoHS Analysis Room in fiscal 2018 to analyze chemical substances contained in procured parts.
Since July 2020, we have made all our products comply with the TSCA-PBT*² regulations, in addition to the PFOA*¹ regulations that were added to the POPs (Persistent Organic Pollutants) regulations. We export 100% compliant products to areas where the regulations are enforced.
*¹ PFOA (Perfluorooctanoic acid)
A type of organofluorine compound that has been identified as a carcinogen
*² TSCA-PBT
A persistent, highly accumulative, toxic substance as defined by the US Toxic Substances Control Act (TSCA)
Environment・Society・Governance
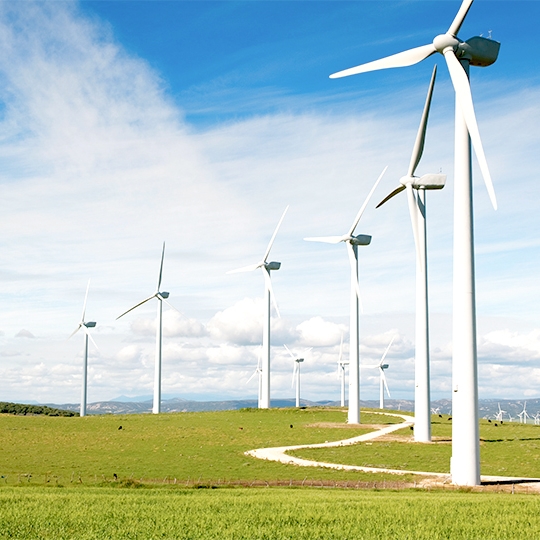
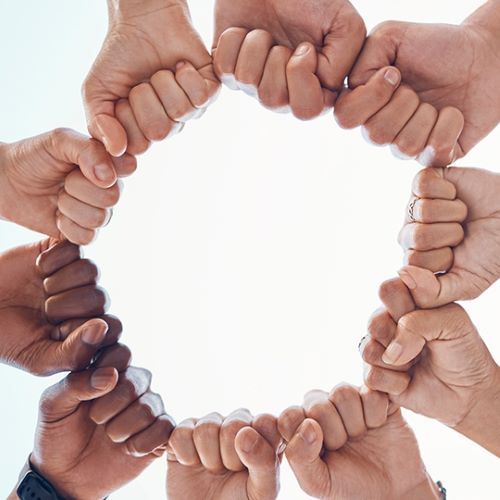
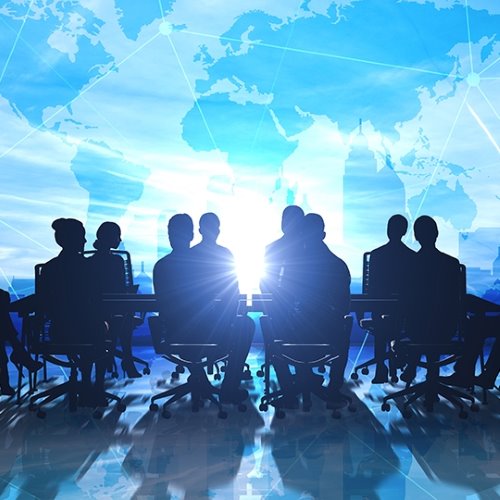