Semiconductor Manufacturing Equipment Business Support Quality
The Semiconductor Company’s CE Department is responsible for maintaining and improving the quality and productivity of the Company’s semiconductor manufacturing equipment used in semiconductor manufacturing and processing processes around the world, from installation setup to maintenance and training support, as well as supplying maintenance parts. In order to contribute to our customers’ profits and increase customer satisfaction by providing high-performance products and high-quality support, we have established a global support structure based on the teamwork of the entire CE Department.
Support Structure
The Semiconductor Company’s Customer Engineering (CE) Department provides a high level of customer responsiveness and value-added services through the Service Division and parts supply without delay through parts centers that enable customers to realize their targeted production.
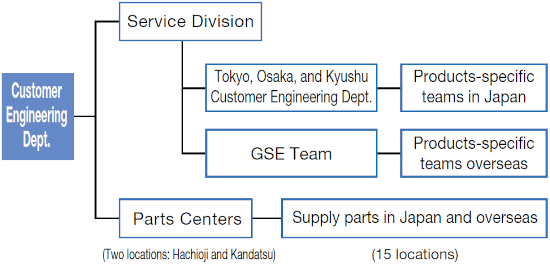
Team (10 persons), parts centers (26 persons)
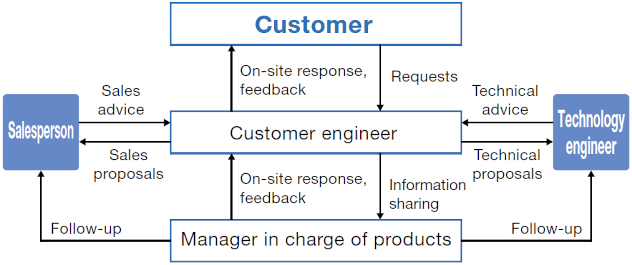
Provision of “Prompt and Meticulous Support”
Aware that it is in the position at the company closest to the customer, the department responds to various requests providing prompt and meticulous support based on the technology and experience it has cultivated. This requires specialized knowledge of products, services, and solutions that are specific to customer specifications. Therefore, in addition to acquiring knowledge about our own products and services, we also deepen our understanding through exposure to operational and system specifications at production sites, such as by conducting product tests from the customer’s perspective. We are building WIN-WIN relationships by providing a level of support that lead to customer satisfaction along with a sense of empathy.
Stable Supply of Parts
We currently supply maintenance parts to customers in approximately 30 countries around the world. In fiscal 2023, we prepared consignment parts for Accretech (Europe) GmbH and Accretech America Inc. to improve delivery time of parts in response to the increase in edge grinder deliveries. Furthermore, we are improving our parts supply structure by registering new parts for inventory at the Kandatsu Plant and reviewing the appropriate inventory counts for the plant.
Education and Training
Qualifications and Training
The Semiconductor Company’s Customer Engineering (CE) Department is required to have a high level of expertise so that it can respond to various customer issues. In order to continue to provide high-quality support, in addition to helping employees acquire qualifications and offering special training, the CE Department is also helping to standardize work levels (accuracy, operation assurance, knowledge, etc.) by conducting training for young engineers and leadership training. In addition, skill sheets are used to clarify the status of employees’ acquisition of knowledge and skills, which is useful for human resource development.
Major Qualifications Acquired and Courses/Exams Taken in FY2023 (Number of Participants)
Qualification acquisition
Handler of Poisonous and Deleterious Substances (1 person), Class B Group 4 Hazardous Materials Engineer (1 person), Class 1 Health Supervisor (1 person)
Special training
Chemical Substances Control Manager Training (1 person), Personal Protective Equipment Manager Training (1 person), Foreman/Health & Safety Manager Training (2 persons), Training for Work Listed in Article 36, Item 32 of the Ordinance on Industrial Safety and Health (2 persons), Training for Work Listed in Article 36, Item 4 of the Ordinance on Industrial Safety and Health (1 person)
Certification Exam
Certification Exam for practical Proficiency in Safety Assurance and Export Control (2 persons): External
Certification Qualifications
All Toyoda Safety and Health Education [person in charge of work] (6 persons), [foreman education] (3 persons), [electric shock / low voltage at height] (8 persons), and safety of industrial robots (3 persons)
Certification test
Lead-free Soldering Certification (1 person): In-house
Global Service Meeting (GSM) Based Training
The GSM, which is held annually by GSE*, was held in a hybrid format, including online, in FY2023 and was attended by 32 service engineer representatives from nine countries and overseas subsidiaries. Each product technical engineer explained new models using actual equipment, new functions, design concepts, and operation processes.
* Global Service Engineers (GSE)
An in-house team that trains and supports overseas service engineers
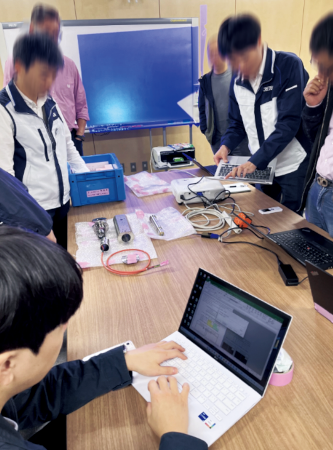
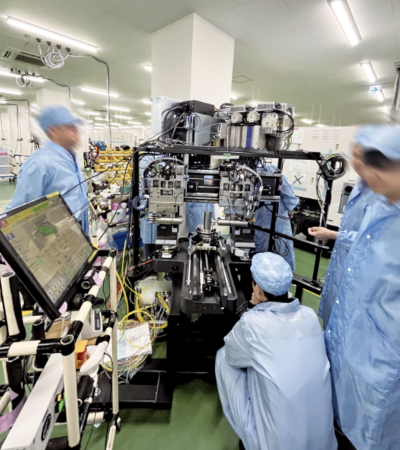
Improvement of Support Quality
Digitalization of Support Services
To promote remote support, we have implemented and enhanced online security measures and established a new dedicated smart glasses* channel at the Hachioji Plant.
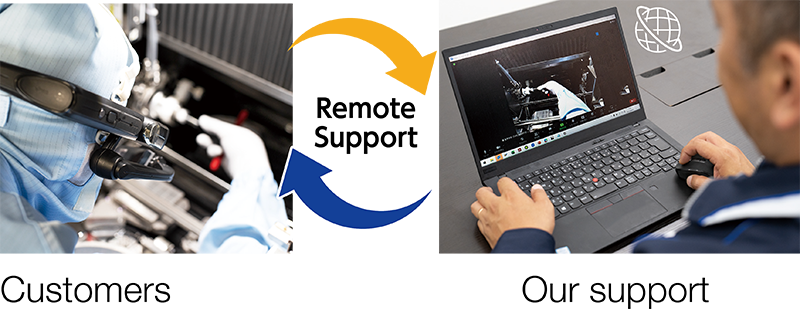
* Smart glasses
Wearable device shaped like spectacles. Information can be displayed on the lenses.
Training Services for Customers
We provide training not only for customers who visit our offices but also at sites around the world to provide equipment operation and maintenance training upon request.
Key Training Services Provided to Customers in FY2023
Probing machine training
12 companies, total of 28 days
Dicing machine training
10 companies, total of 11 days
High-rigidity grinder training
1 company, total of 4 days
CMP (Chemical Mechanical Polishing) training
2 companies, total of 4 days
Provided Help and Support for Customers Affected by the 2024 Noto Peninsula Earthquake
We collaborated with our service and management staff in charge to quickly assess the extent of damage to customers affected by the major earthquake that struck the Noto Peninsula in Ishikawa Prefecture on January 1, 2024, and shared information with those customers. In addition, we prioritized everything from troubleshooting to recovery according to the customer’s circumstances, and conducted management and provided support until the final completion dates.
Environment・Society・Governance
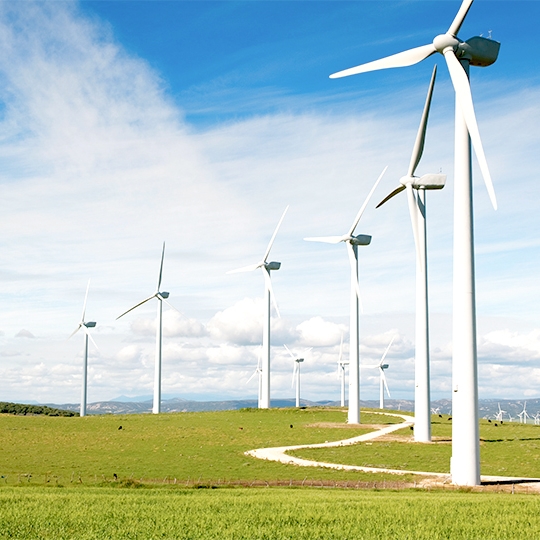
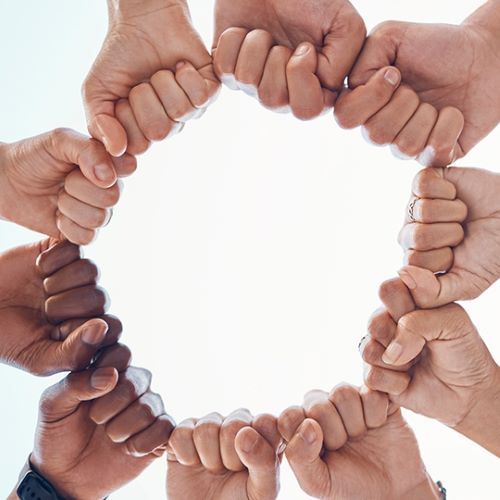
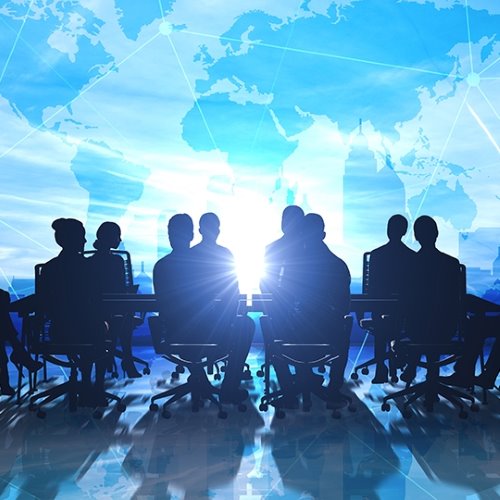