Occupational Health and Safety
Many devices, parts, tools, and processing machines from the Tokyo Seimitsu Group, a manufacturer of machinery, can be found at manufacturing and distribution sites. As our products consist of equipment used in production, many tasks such as delivery, installation, maintenance, and inspection occur in the unfamiliar environments of customers’ production sites. By carefully investigating risks associated with these tasks, observing and predicting the movement and flowline of workers, and implementing measures to minimize safety risks, we promote occupational health and safety initiatives so that everyday work actions can be carried out safely and rationally.
Targets and Results
Target | FY2020 | FY2021 | FY2022 | FY2023 | |
Accidents resulting in leave (incidents) | 0 | 0 | 2 | 1 | 4 |
Accidents not resulting in leave (incidents) |
0 | 6 | 10 | 12 | 15 |
Scope: Employees and temporary employees of the Semiconductor Company, Metrology Company, and Administration Company, Tokyo Seimitsu
Occupational Accidents
By accident type, “caught in or compressed by equipment or objects” and “falls” accounted for the majority of accidents in fiscal 2023. In order to prevent falls, we will promote initiatives such as making employees aware that walking while using a smartphone is prohibited in the workplace, enforcing organization and tidiness, and strengthening workplace patrols to prevent tripping during work.
Accidents by Type
Type |
Number of occupational accidents |
Number of injuries or |
Flying or falling objects |
2 |
2 |
Cuts or abrasions |
4 |
4 |
Being caught |
6 |
6 |
Falling |
5 |
5 |
Colliding |
0 |
0 |
Overexertion |
1 |
1 |
Scope: Employees and temporary employees of the Semiconductor Company, Metrology Company, and Administration Company, Tokyo Seimitsu
Indicator Monitoring
Tokyo Seimitsu uses accident frequency rate and severity rate as indicators to evaluate the occurrence of occupational accidents.
We monitor annual results and the occurrence of occupational accidents at manufacturing companies (companies with over 100 employees).
Frequency Rate for Accidents Resulting in Leave*¹
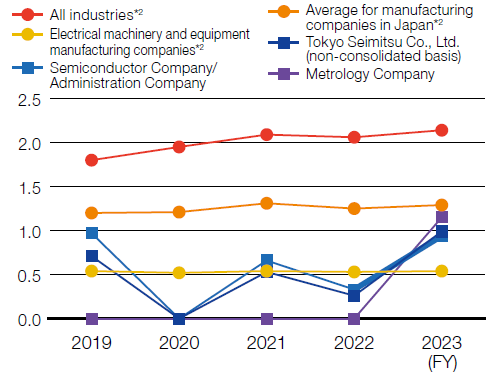
FY2019 | FY2020 | FY2021 | FY2022 | FY2023 | |
All industries*² | 1.80 | 1.95 | 2.09 | 2.06 | 2.14 |
Average for manufacturing companies in Japan*² |
1.20 | 1.21 | 1.31 | 1.25 | 1.29 |
Electrical machinery and equipment manufacturing companies*² |
0.54 | 0.52 | 0.54 | 0.53 | 0.54 |
Tokyo Seimitsu Co., Ltd. |
0.71 | 0.00 | 0.53 | 0.26 | 0.99 |
Semiconductor Company/ Administration Company |
0.97 | 0.00 | 0.66 | 0.33 | 0.94 |
Metrology Company | 0.00 | 0.00 | 0.00 | 0.00 | 1.15 |
*¹ Frequency rate: Indicates the frequency of injury or death due to occupational accidents.
Formula: (Casualties / total hours worked) × 1,000,000
*² Ministry of Health, Labour and Welfare (Survey on Industrial Accidents)
Severity Rate for Accidents Resulting in Leave*¹
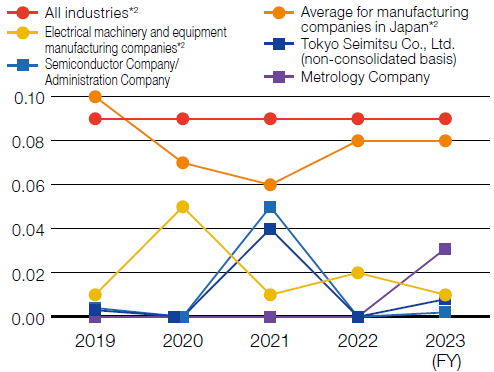
FY2019 | FY2020 | FY2021 | FY2022 | FY2023 | |
All industries*² | 0.09 | 0.09 | 0.09 | 0.09 | 0.09 |
Average for manufacturing companies in Japan*² |
0.10 | 0.07 | 0.06 | 0.08 | 0.08 |
Electrical machinery and equipment manufacturing companies*² |
0.01 | 0.05 | 0.01 | 0.02 | 0.01 |
Tokyo Seimitsu Co., Ltd. |
0.003 | 0.000 | 0.040 | 0.000 | 0.008 |
Semiconductor Company/ Administration Company |
0.004 | 0.000 | 0.050 | 0.000 | 0.002 |
Metrology Company | 0.000 | 0.000 | 0.000 | 0.000 | 0.031 |
*¹ Severity rate: Percentage of the degree of loss caused by occupational accidents.
Formula: (Total lost workdays / total hours worked) × 1,000
*² Ministry of Health, Labour and Welfare (Survey on Industrial Accidents)
Occupational Health and Safety Promotion Structure
At the Hachioji, Hanno, and Tsuchiura plants, we have established the Safety and Health Committee, with each plant manager serving as the general safety and health manager. The committee plans and deliberates on major health- and safety-related matters in a bid to maintain and improve a safe and comfortable work environment. To raise employees’ awareness of health and safety in the workplace and in the interest of maintaining and promoting their health, the committee meets once a month, in principle, and on an ad hoc basis when the general safety and health manager deems necessary. In fiscal 2023, the Safety and Health Committee met as scheduled. At the Furudono Plant, which is a small-scale worksite with fewer than 50 employees, the Plant Manager promotes workplace health and safety as a health promoter, and participates in and reports on the Safety and Health Committee of the Tsuchiura Plant. We also conduct internal audits twice a year, with results submitted to the Audit Department and reported to the Board of Directors. The Health and Safety Committee is subject to audits by the Audit Department.
Safety and Health Committee
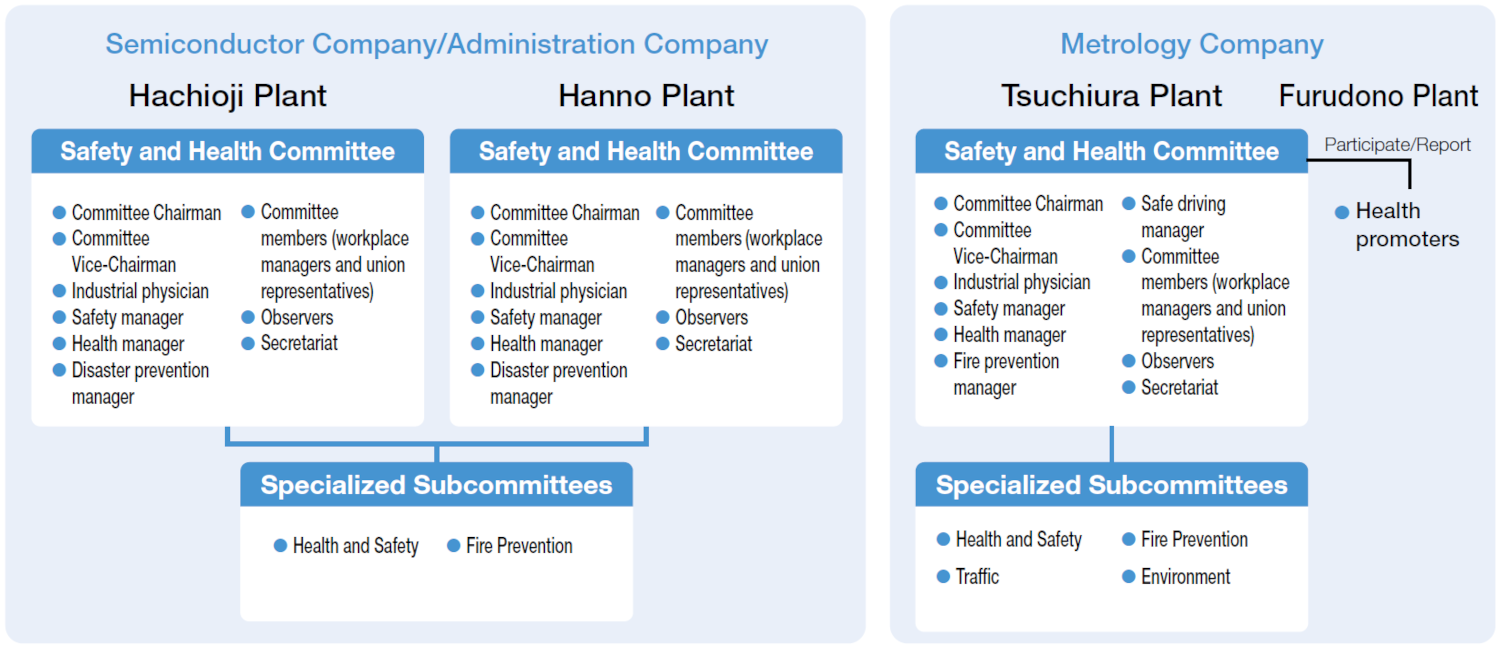
In addition, each plant has appointed a Chemical Substances Control Manager and a Personal Protective Equipment Manager.
Number of Safety and Health Committee Meetings Held in FY2023
Hachioji Plant Safety and Health Committee
met 12 times
Hanno Plant Safety and Health Committee
met 7 times*¹
Tsuchiura Plant Safety and Health Committee
met 12 times
Participation by Furudono Plant health promoters
met 6 times*²
*¹ Number of meetings held since the completion of the Hanno Plant in July 2023
*² Number of times health promoters participate in meetings since operations were transferred to the Furudono Plant in October 2023
Patrol Activities
Workplace Patrols Conducted by Health Supervisors
At the Hachioji Plant and Hanno Plant, health supervisors generally conduct weekly workplace patrols to check equipment, work methods, and hygiene conditions, and take necessary measures. Patrol records for which health supervisor workplace patrol checklists are used are submitted to the General Affairs Section and kept for five years.
Installation of equipment to prevent shelf from tipping over
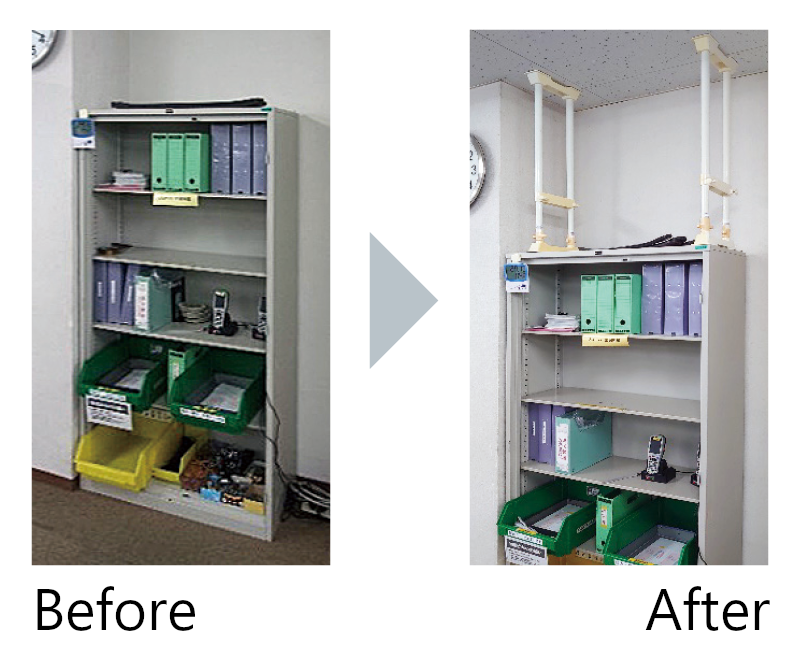
Measure to prevent rack load
from collapsing
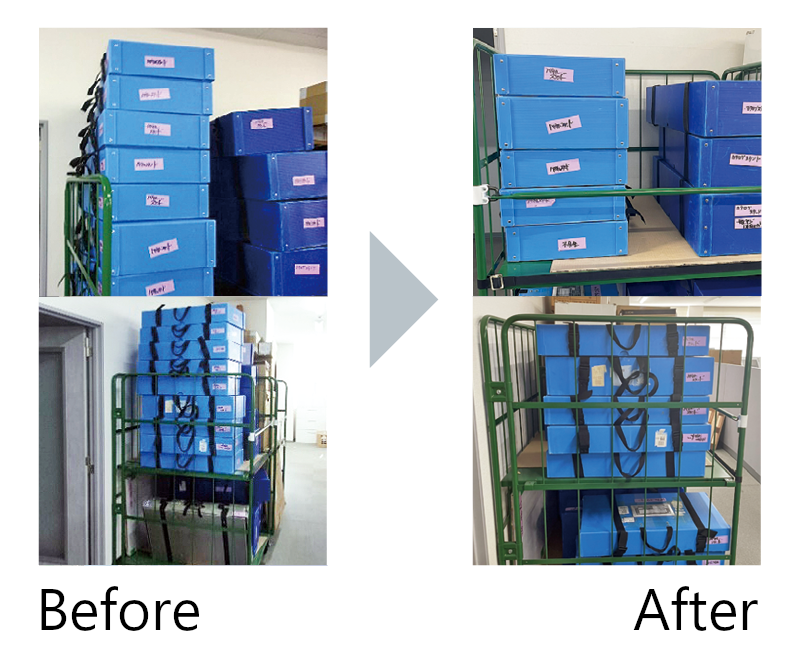
5S* Patrols and Safety Patrols
At the Tsuchiura Plant, managers and general staff conduct weekly 5S patrols, while the Health and Safety Subcommittee members perform monthly safety patrols. In cases where improvements are needed, follow-up patrols are conducted after the improvements are proposed to confirm the effectiveness of the patrols.
* 5S (A slogan for maintenance and improvement of workplace environments)
It stands for sort (seiri), set in order (seiton), shine (seisou), standardize (seiketsu), and sustain (shitsuke)
Repair of steel floor panel
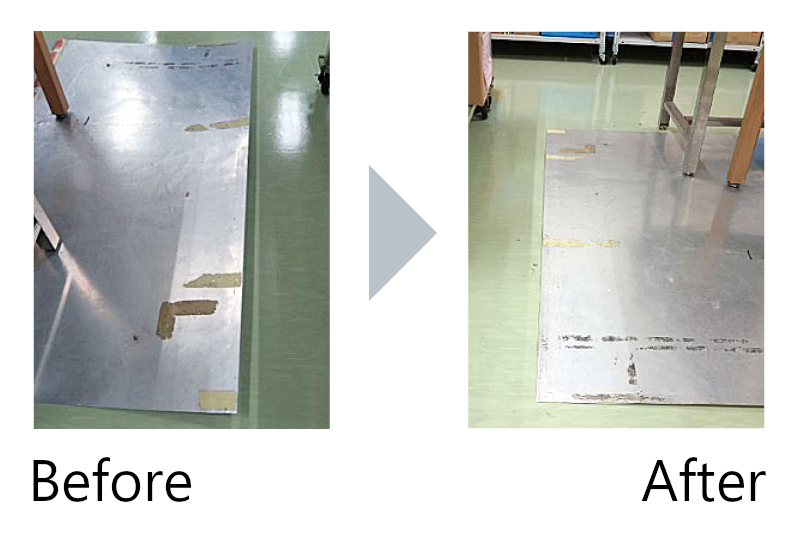
Measure to prevent items from piling up
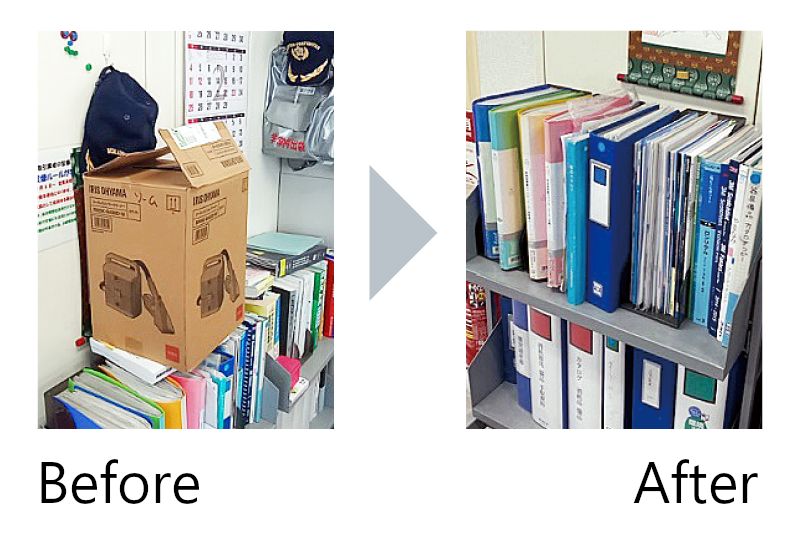
Risk Assessments at Work Sites
We regularly conduct risk assessments by conducting workplace inspections to check working environments and identify issues. This leads to the creation of measures for dealing with these issues and brings about improvements. In addition to risk assessments performed when introducing new machinery or changing work procedures, we work to avoid risk by conducting education and training on machinery operation, heavy equipment work, wiring operation, and other topics as needed.
Number of risk assessments conducted when introducing new equipment in accordance with equipment risk assessment implementation standards
26
Number of work risk assessments conducted in accordance with work risk assessment regulations
43
Risk Assessment Training
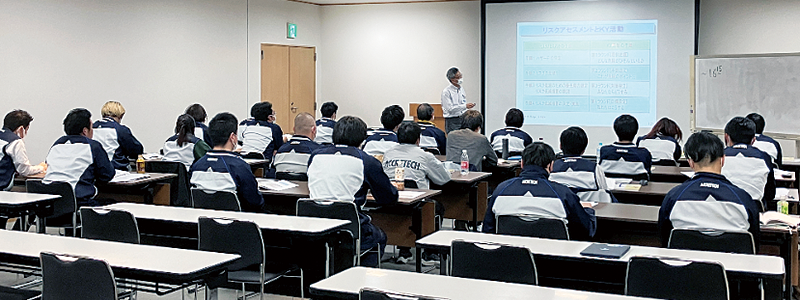
At the Hachioji Plant, risk assessment training is conducted by outside instructors to prevent occupational accidents. In fiscal 2023, the risk assessment training was held twice, providing opportunities for more practical learning on risk assessment methods and the construction of a safety management system through classroom lectures and group work.
Education and Training
In-house Training and Testing
We conduct in-house training and certification testing to help employees avoid hazards in a variety of situations, including commuting, traveling, and working in the plant.
Course Content in Fiscal 2023 |
Number of attendees |
Traffic safety seminar | 942 |
Lifesaving first aid training | 15 |
Risk assessment training | 65 |
High Pressure Gas Safety Training Seminar | 0 |
Special training on low voltage electricity handling | 34 |
In-house forklift certification exam (Hachioji Plant) | 13 |
Forklift, sling work, crane safety training |
63 |
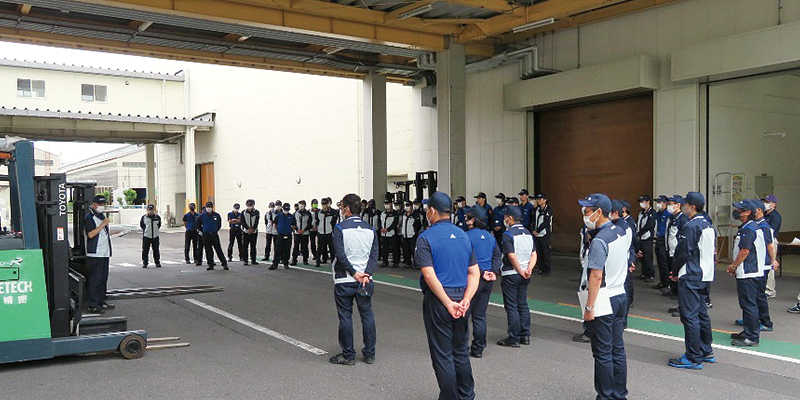
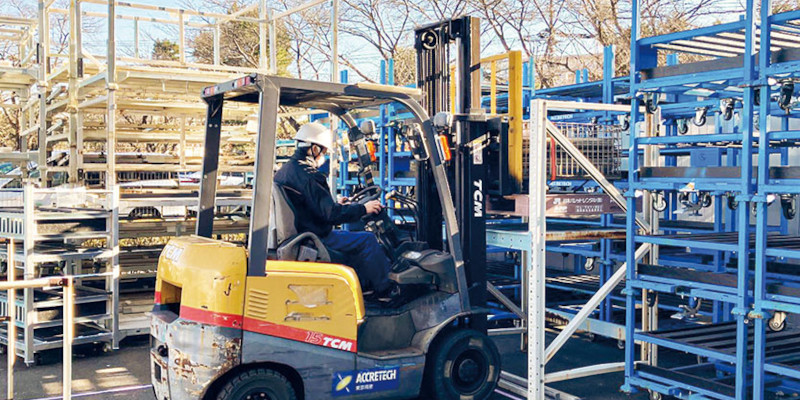
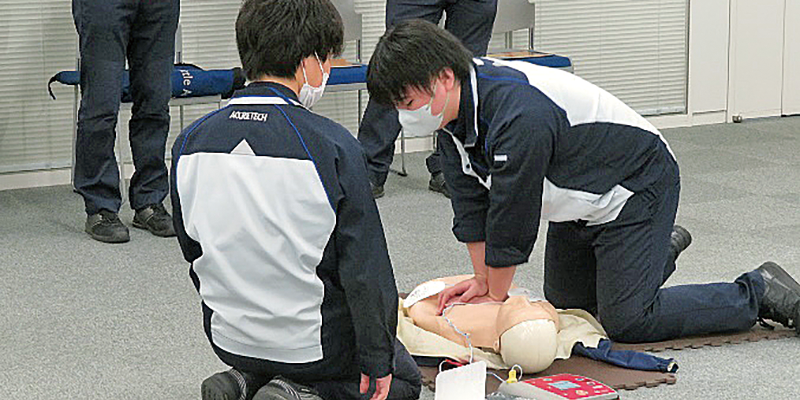
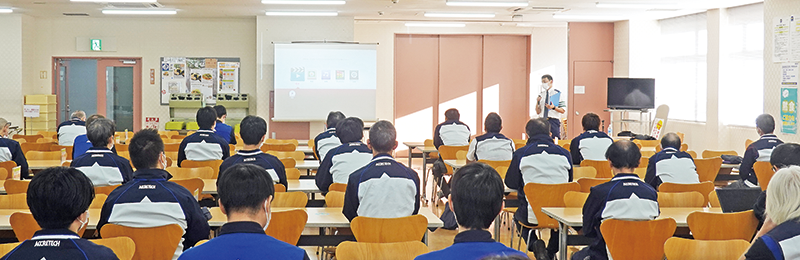
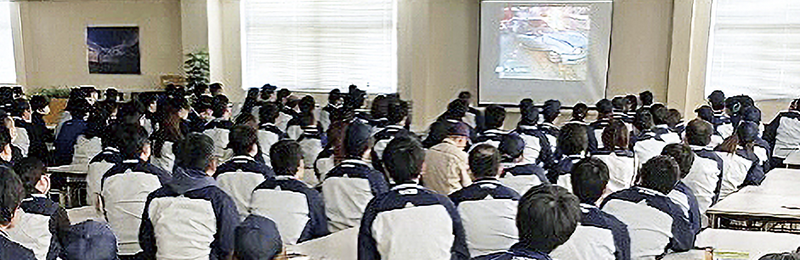
External Training
Tokyo Federation of Labor Standards Associations, Hachioji Branch
In order to promote activities to prevent industrial accidents among local workers, we participate in seminars held by the Tokyo Federation of Labor Standards Associations, Hachioji Branch. These seminars are designed for participants to acquire the skills necessary to engage in work. Employees who have completed the seminars take in-house practical tests tailored to factory environments for thorough health and safety education.
Content of Courses Conducted by the Tokyo |
Number of attendees |
Training course for sling and crane operators | 26 |
Foremen and safety and health supervisors | 15 |
Operation chief of organic solvents | 22 |
Skill training course for chief of specified chemical |
12 |
Handling of dangerous substances Class B Type 4 | 5 |
Advanced lifesaving skills | 2 |
Self-defense firefighting | 4 |
Fire and disaster prevention manager | 1 |
Full harness | 3 |
Forklift | 6 |
Power press | 0 |
Aerial work platform operation training | 1 |
Gas welding | 3 |
Locations covered: Tokyo Seimitsu Hachioji Plant, Hanno Plant, Tsuchiura Plant, and Furudono Plant
Semiconductor Equipment Association of Japan (SEAJ)
The Semiconductor Equipment Association of Japan promotes “SEAJ recommended safety training” an industrial standard for safety training of personnel involved in the installation, maintenance, and servicing of semiconductor manufacturing equipment. At the Hachioji Plant, our employees who belong to Semiconductor Equipment Association of Japan’s Safety Training Subcommittee conduct online-based “SEAJ Work Safety Seminars” for Semiconductor Company CE Department employees and manufacturing and design engineers who work on the manufacturing floor or in clean rooms. A total of 458 employees have participated in the seminar so far.
FY2023 SEAJ Recommended Safety Training | Number of attendees |
New attendees | 28 |
Attendees for recertification (required to attend every three years) |
140 |
Disaster and Accident Prevention
Self-Defense Fire Drill
Every year, the Disaster Prevention Subcommittee under the Safety and Health Committee plans and conducts emergency evacuation drills for all plant employees, including those working at subsidiaries and affiliated companies within our plants.
FY2023 Evacuation Drills
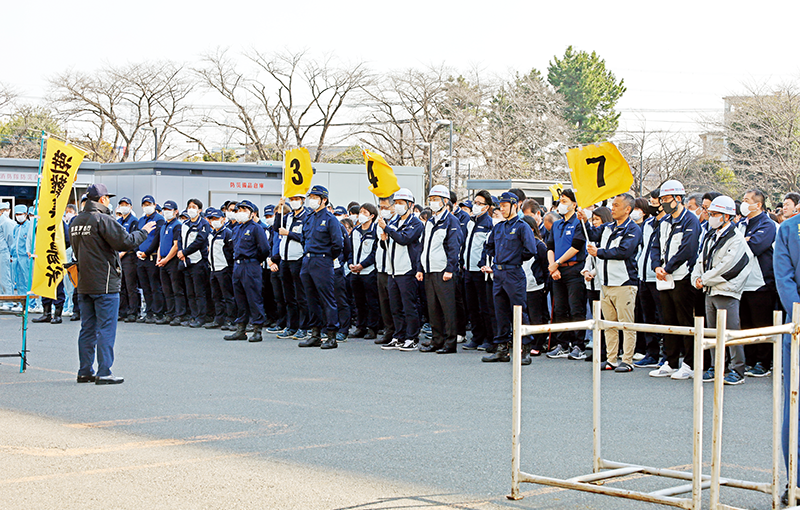
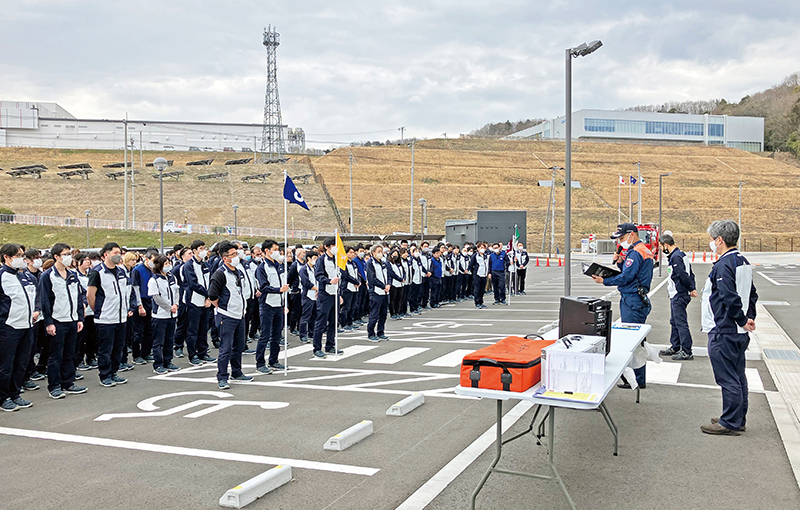
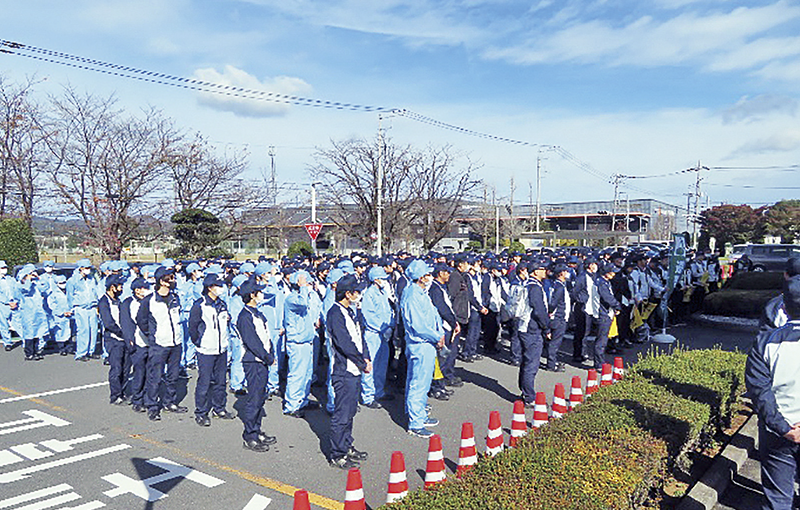
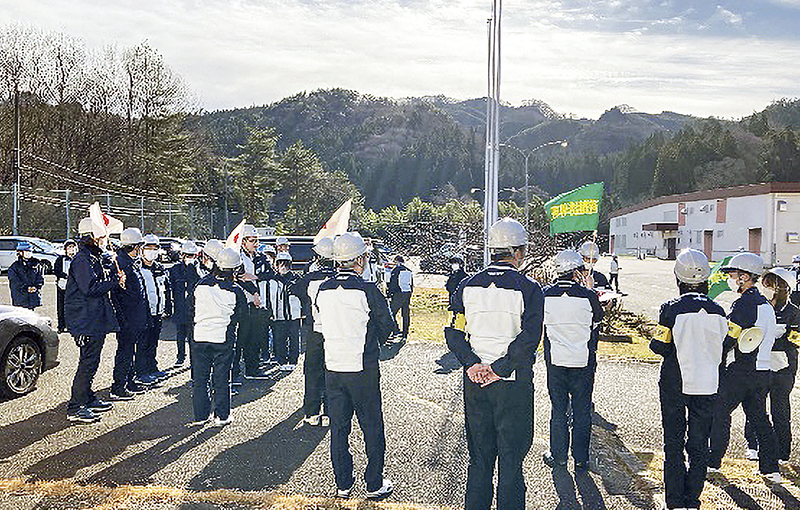
Fire Drills
At the Hachioji, Hanno, and Tsuchiura plants, we organize self-defense fire brigades and conduct regular training one or two times a month according to annual plans. The Company also participates in an annual “self-defense firefighting training review” hosted by the Hachioji Fire Department and the Hachioji Fire Prevention Management Study Group. In this competition, self-defense fire brigades from business establishments in the city gather to compete in a heated competition to test the effectiveness of their daily training based on speed and accuracy of indoor fire hydrant operation. Forty-four teams comprised of men and women from business offices in Hachioji City participated in the self-defense firefighting training review for fiscal 2023. Our self-defense fire brigade from the Hachioji Plant competed in the “No. 1 Fire Hydrant, Male Group B” category.
FY2023 Self-Defense Firefighting Training Review
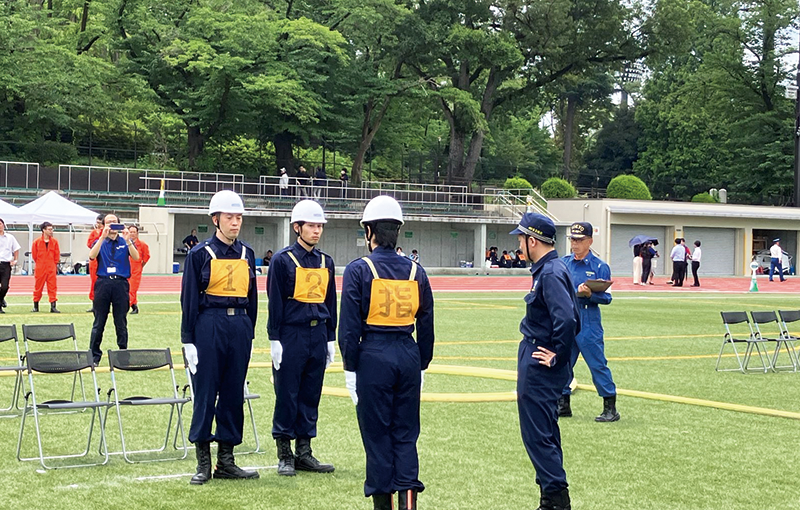
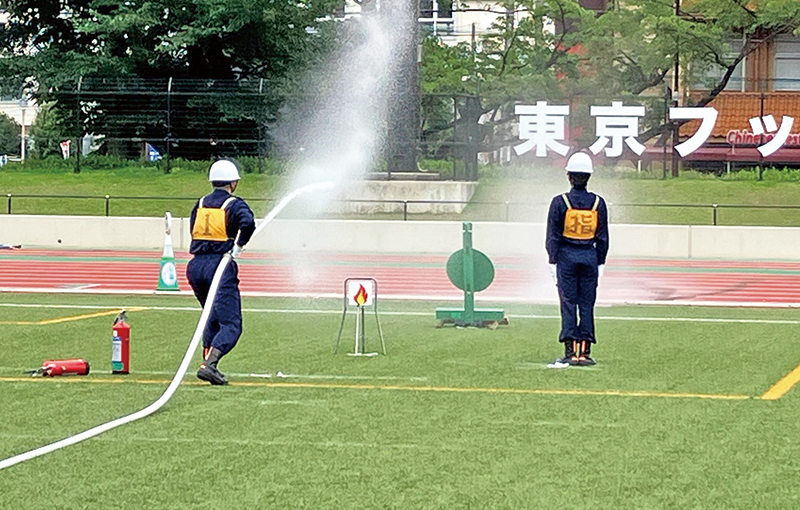
Self-Defense Fire Brigade Training at Each Plant
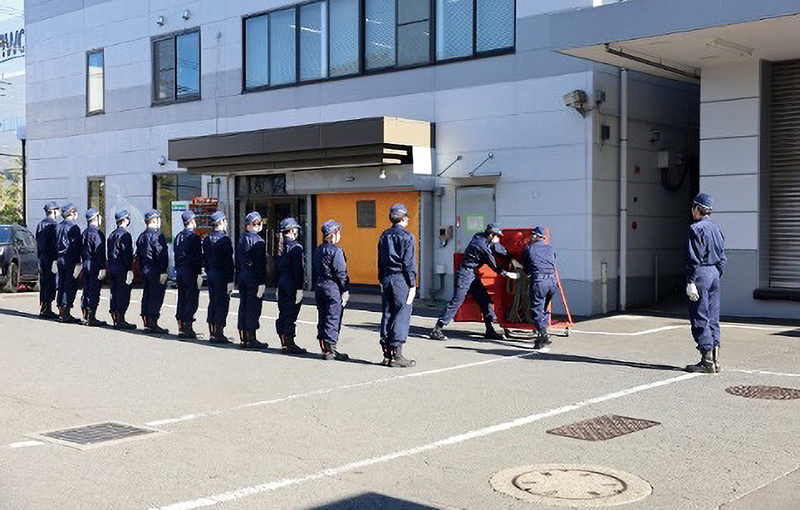
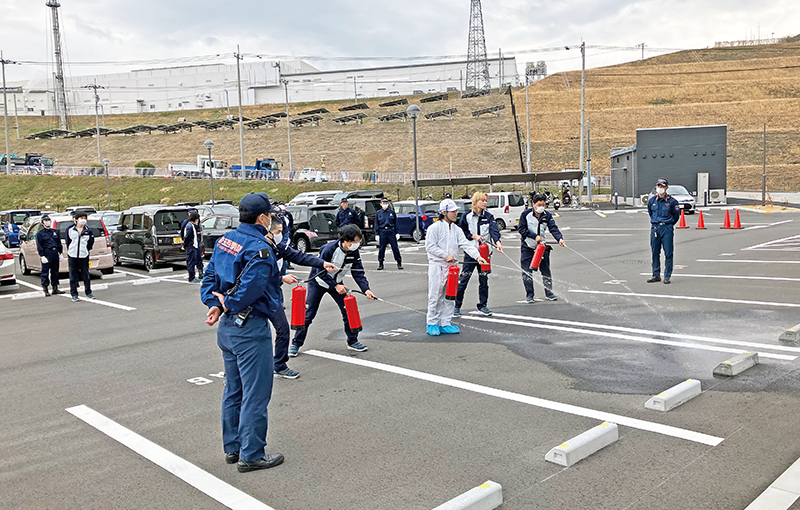
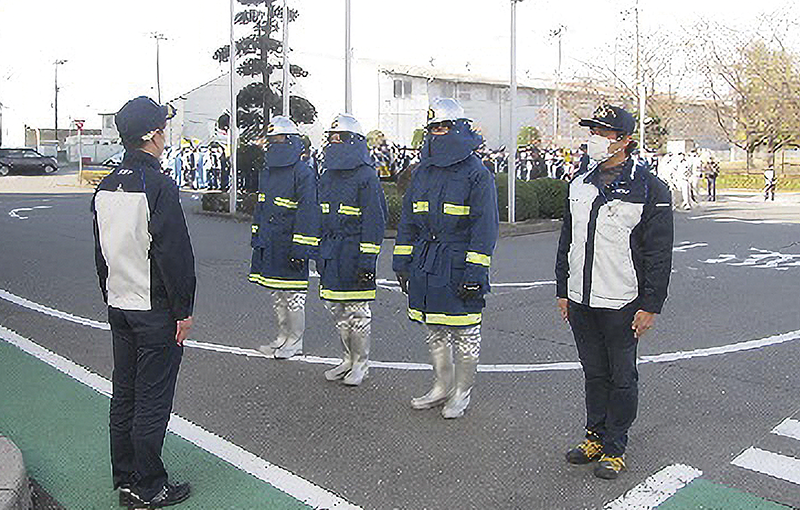
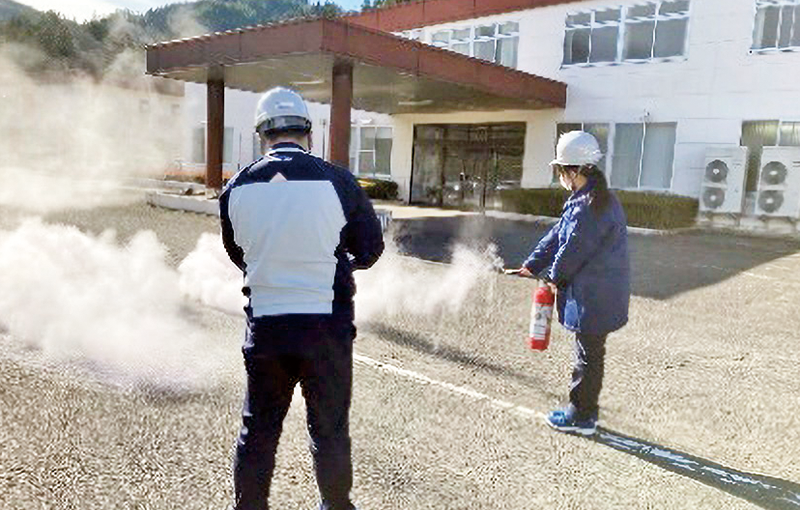
Emergency Scenario Training
Emergency scenario training is conducted at least once a year at each plant so that appropriate tasks, such as recovery/ cleaning, can be carried out in the event of a hazardous substance leak or splash-based accident. Each division that handles hazardous substances submits a training plan to the person responsible for environmental management at the beginning of the relevant term and submits a report after the training is conducted. In fiscal 2023, the Hachioji Plant conducted training 36 times for 13 divisions. At the Tsuchiura Plant, 160 people from the plant department took part in “chemical cleaning agent splash prevention training.”
Training for Leakage of Chemical Substances with High Alkaline Content (Hachioji Plant)
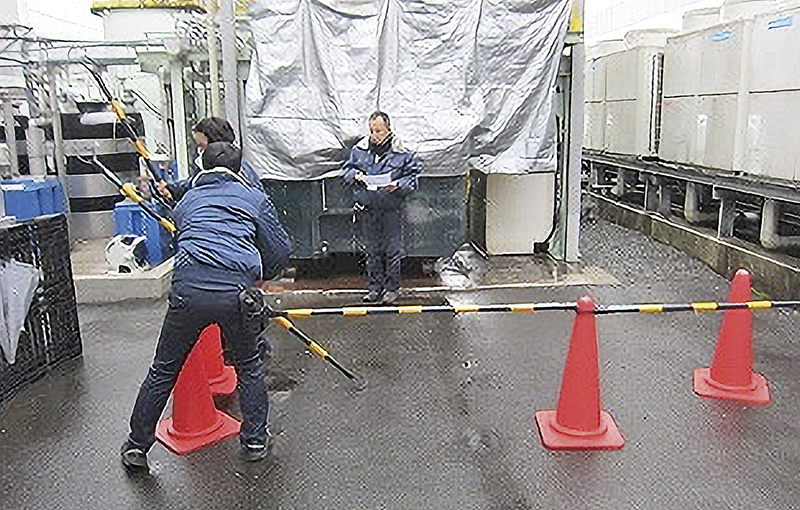
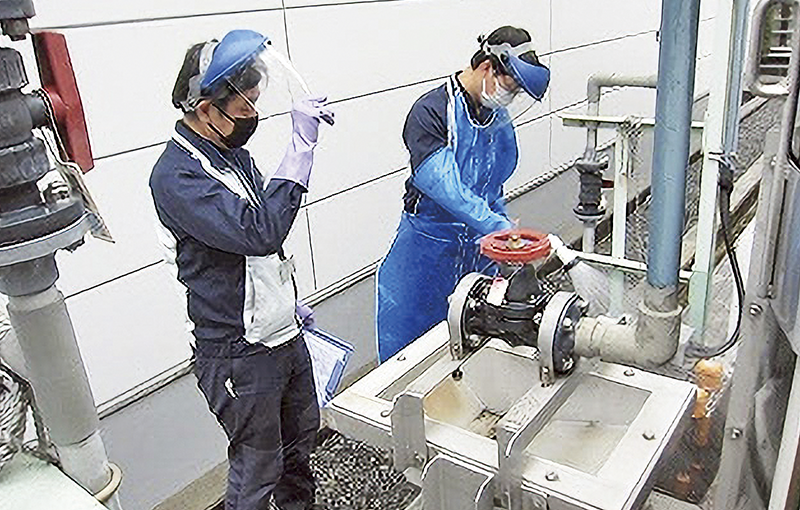
Chemical Cleaning Agent Splash Scenario Training (Tsuchiura Plant)
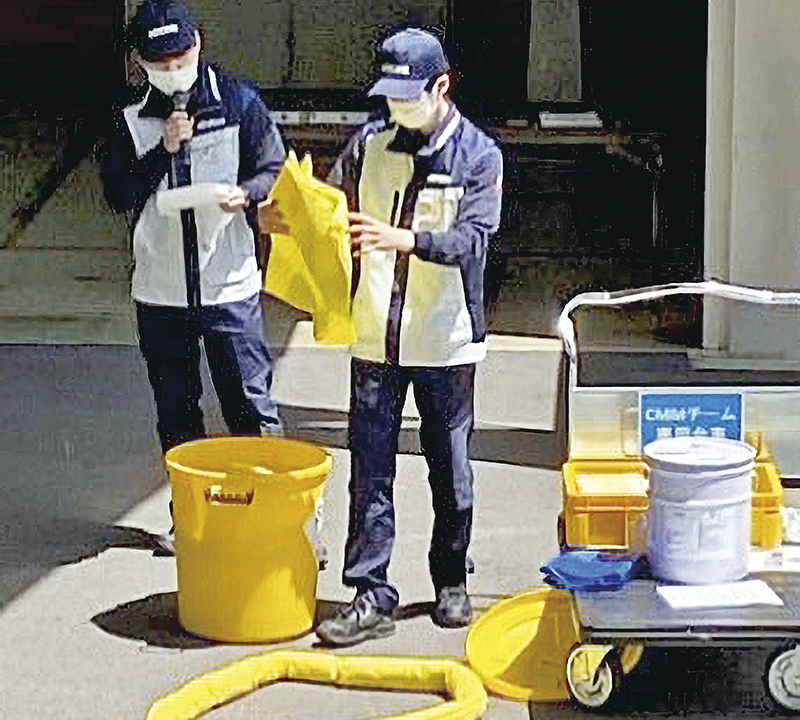
Handling of Chemicals and Chemical Substances
When considering the purchase of industrial chemicals, we conduct a chemical substance risk assessment to check for the presence of contained environmental pollutants (organic solvents, specified chemical substances, hazardous materials, etc.), in accordance with our internal regulations. The department in charge of this matter at the Hachioji Plant decides whether to purchase the chemicals based on the results of assessments conducted at the Hachioji, Hanno, and Tsuchiura plants. In fiscal 2023, 118 chemical substance risk assessments were conducted for newly adopted chemicals and to review chemicals already in use. We require divisions that manage and use chemical substances to conduct regular inspections and regular quantity checks.
The Company is also promoting the reduction and substitution of chemical substances in accordance with the PRTR Act, Ordinance on Prevention of Organic Solvent Poisoning, and the Poisonous and Deleterious Substances Control Act. In addition, we carry out patrols to check the status of chemical management and storage and the supplies used to prevent chemical leaks through the Regulated Substance Control Working Group under the Safety and Health Committee.
Environment・Society・Governance
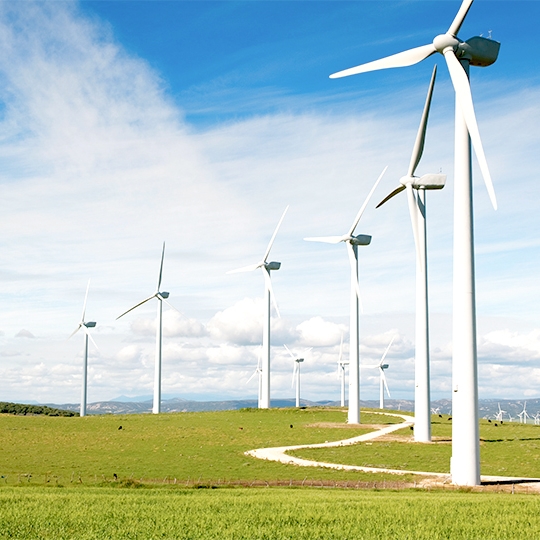
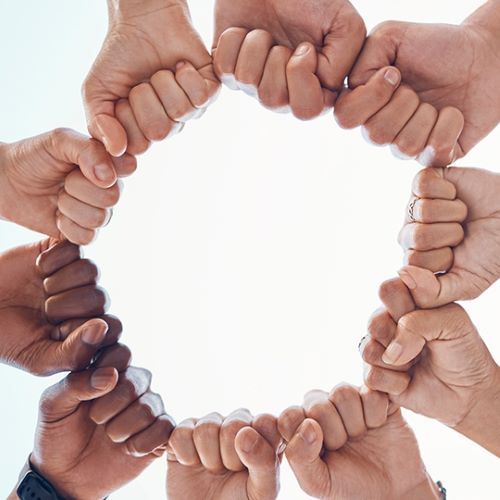
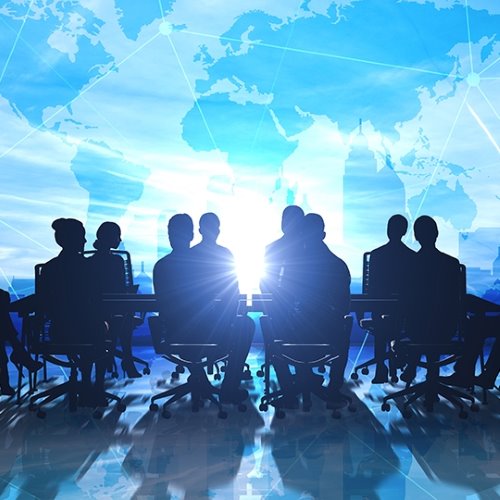